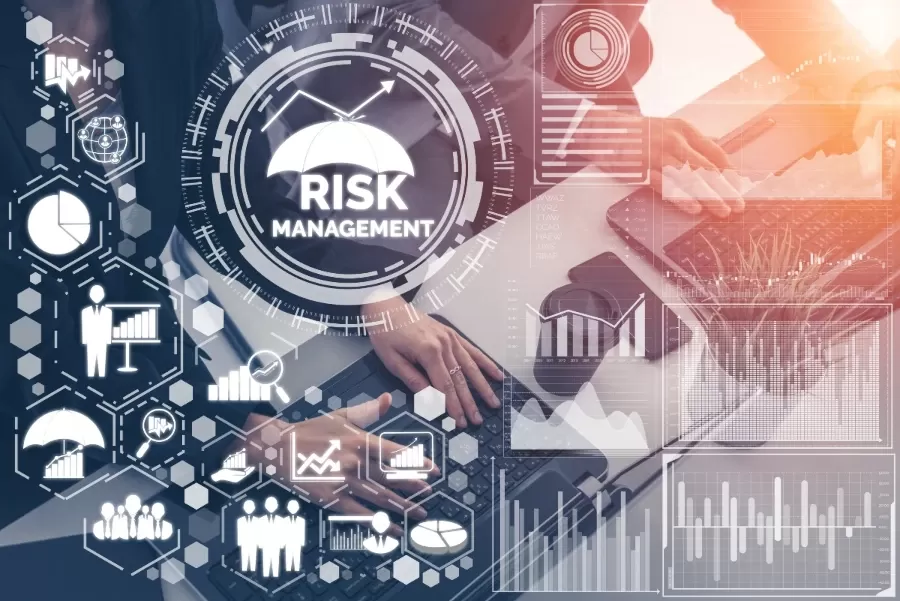
PONOWNA OCENA RYZYKA MASZYNY – NA CZYM POLEGA?
Ocena ryzyka technicznego maszyny jest jednym z najważniejszych obowiązków, jakie na producentów lub upoważnionych przez nich przedstawicieli nakłada dyrektywa maszynowa 2006/42/WE. Zgodnie z jej wytycznymi analiza ryzyka nie jest jednak zamkniętym etapem produkcji, a procesem, który powinien się rozpocząć już na etapie projektowania, a skończyć tuż przed samym dopuszczeniem jej do obrotu.
Nie można się więc opierać na pierwotnych założeniach bezpieczeństwa. Tuż po montażu maszyny i integracji systemu bezpieczeństwa jest konieczne wykonanie ponownej oceny ryzyka.
Sprawdź, jak prawidłowo dokonać walidacji wprowadzonych rozwiązań, co powinna obejmować ponowna ocena ryzyka i jakie kroki może podjąć producent, jeśli analiza ujawni niezadowalający poziom bezpieczeństwa.
Dlaczego należy wykonać ponowną ocenę ryzyka?
Norma PN-EN ISO 12100 wymienia szereg zagrożeń, które mogą występować w związku z obsługą maszyn. Dokument dzieli zagrożenia związane z obsługą maszyny na kilka kategorii, w tym:
- mechaniczne;
- elektryczne;
- termiczne;
- związane z hałasem;
- związane z wibracjami;
- związane z materiałami i substancjami szkodliwymi dla zdrowia;
- związane z promieniowaniem;
- spowodowane przez maszynę nieprawidłowo zaprojektowaną pod względem ergonomii.
Ta klasyfikacja pozwala jednak stworzyć tylko wstępną listę zagrożeń, które należy rozpatrzyć dla konkretnej maszyny. Nie przewiduje wszystkich możliwych sytuacji, które mogą wystąpić podczas jej obsługi.
Warto też przy tym pamiętać, że zagrożenia są najczęściej unikalne dla maszyny. W związku z tym w większości przypadków nie jest możliwe stworzenie zamkniętego katalogu zagrożeń już na etapie projektowania, a duża część z nich nie zostanie ujawniona bez przeprowadzenia testów i symulacji. Zresztą, ta sama norma wskazuje, że lista zagrożeń powinna być uzupełniania w miarę postępów prac.
Z tych powodów wykonanie ponownej oceny ryzyka jest nieodzowne i pozwala wykryć zagrożenia podczas każdego cyklu pracy maszyny, tj. jej uruchomienia, produkcji, konserwacji czy naprawy.
Jakie elementy wchodzą w skład ponownej oceny ryzyka maszyny?
Celem ponownej oceny ryzyka maszyny jest analiza poprawności założeń koncepcji bezpieczeństwa i poprawności wprowadzenia zastosowanych rozwiązań.
Powinna odpowiadać na pytania takie jak:
- Czy maszyna została zaprojektowana zgodnie z przepisami?
- Czy uzyskany poziom ryzyka jest zadowalający, a jeśli nie, to czy można je zmniejszyć za pomocą dostępnych środków?
- Czy środki ochronne zostały zastosowane prawidłowo?
- Czy zastosowanie elementów konstrukcyjnych bezpiecznych samych w sobie i środków ochronnych nie zmniejsza wydajności maszyny i nie utrudnia pracy operatora?
- Czy w trakcie ponownej oceny ryzyka zostały ujawnione nowe zagrożenia i czy można im zapobiec za pomocą dostępnych środków?
Ponownej oceny ryzyka nie można ograniczać wyłącznie do jednej metody. Aby weryfikacja była zgodna z wymaganiami dotyczącymi bezpieczeństwa, musi obejmować działania takie jak:
- oględziny maszyny w stanie spoczynku;
- obserwację urządzenia podczas pracy;
- pomiary parametrów maszyny podczas pracy;
- symulację usterek w systemie bezpieczeństwa;
- przegląd informacji dotyczących sposobów jej użytkowania i sprawdzenie ich w praktyce.
Ważne jest, aby wszystkie testy i badania zostały odpowiednio zarejestrowane i udokumentowane.
Co, jeśli ponowna ocena ryzyka ujawni uchybienia projektowe?
Akty prawne, które wyznaczają standardy oceny ryzyka maszynowego oraz założenia, które należy spełnić, aby maszyna została uznana za bezpieczną, to dyrektywa maszynowa 2006/42/WE oraz zharmonizowane z nią normy, głównie PN-EN ISO 12100:2012 Bezpieczeństwo maszyn. Ogólne zasady projektowania. Ocena ryzyka i zmniejszanie ryzyka. Są one punktem odniesienia dla większości jednostek, które są odpowiedzialne za wystawienie deklaracji zgodności WE.
Te dokumenty nakreślają dobre praktyki, dostarczają wskazówek co do przeprowadzenia ponownej oceny ryzyka i rozwiązywania konkretnych problemów związanych z bezpieczeństwem. Są jednak dość ogólne i nie wyznaczają konkretnych metod i sposobów ponownej oceny ryzyka. W takim przypadku producent musi bazować na swojej wiedzy i doświadczeniu.
Znając jednak jej główne założenia, można ustalić ogólny sposób postępowania i kolejność podejmowanych kroków. Dyrektywa maszynowa wskazuje, że w celu zapewnienia maksymalnego bezpieczeństwa producent ma obowiązek wykorzystać wszystkie dostępne środki i określa ich pierwszeństwo.
Począwszy od najważniejszych te środki to:
- elementy konstrukcyjne bezpieczne same w sobie;
- dodatkowe środki techniczne, które w istotny sposób zmniejszają ryzyko maszynowe (np. osłony, kurtyny świetlne i laserowe, wyłączniki bezpieczeństwa);
- poinformowanie użytkowników o ryzyku resztkowym.
Wyeliminowanie lub zmniejszenie ryzyka powinno więc przebiegać dokładnie w takiej samej kolejności. Nie można zrezygnować z jakiegokolwiek elementu konstrukcyjnego na rzecz technicznych środków ochronnych np. z powodów finansowych. Podobnie nie jest dopuszczalne samo informowanie użytkownika o ryzyku resztkowym, jeśli to ryzyko można wyeliminować za pomocą środków technicznych lub bezpiecznych konstrukcji.
Jeśli zatem ponowna ocena ryzyka wskaże, że poziom bezpieczeństwa jest niezadowalający, pierwszym krokiem producenta powinna być modyfikacja pierwotnego projektu w zakresie konstrukcji bezpiecznych samych w sobie. Dopiero jeśli nie jest to możliwe, można rozpatrzyć zmniejszenie poziomu ryzyka poprzez techniczne środki ochronne. Jest to jedyny sposób na zapewnienie bezpieczeństwa pracy w zakładzie przemysłowym.